Industrial Smart Working
Il concetto di “resilienza” è sulla bocca di tutti ed è ormai una prerogativa necessaria e sufficiente per poter confermare l’esistenza di una qualunque organizzazione sul mercato
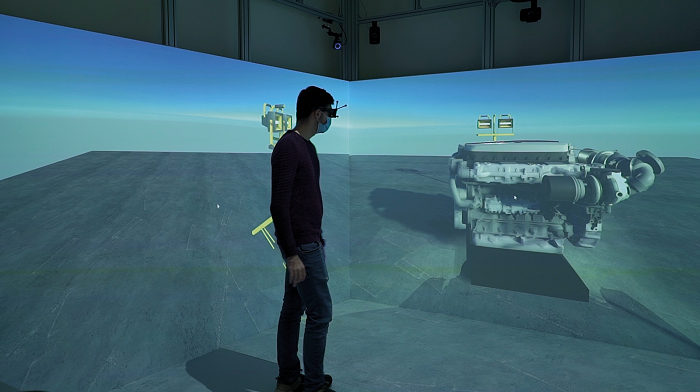
Federica Acerbi
Marco Spaltini
Dottorandi Dipartimento di Ingegneria gestionale del Politecnico di Milano - Gruppo di ricerca SoM Manufacturing Group
È chiaro come la nostra società, nel suo complesso, abbia dovuto adeguarsi velocemente a un cambio radicale, spinto in particolar modo dalla pandemia del Covid-19. Questi eventi hanno forzato le aziende a modificare la loro quotidianità, il loro layout interno e i loro core business (ad esempio producendo mascherine per far fronte al nuovo bisogno, anche se limitato nel tempo) per un periodo che in quel momento non aveva scadenza, ma solo data di inizio.
Tra tutti, nel febbraio 2020, il settore manifatturiero si è trovato a dover conciliare due spinte di trasformazione che, se mal governate, avrebbero potuto compromettere la sopravvivenza di diverse aziende: da un lato l’innovazione tecnologica supportata dalla diffusione delle tecnologie di Industria 4.0 e i relativi ingenti investimenti, dall’altro la trasformazione delle attività e dell’organizzazione interna ed esterna alle aziende, necessaria a fronteggiare le esigenze della pandemia. Nonostante i primi timidi riscontri, ci si è resi conto molto presto di quanto gli investimenti nel 4.0 fossero preziosi per mantenere alto il nome dell’azienda.
Considerata la necessità, in primis, di garantire il distanziamento sociale anche all’interno dei luoghi di lavoro, si è subito posta l’attenzione sul riorganizzare le attività interne e garantire spazi adeguati a ciascun lavoratore sia in ufficio che in reparto. Si è soliti pensare che questa necessità possa essere facilmente risolta dall’ormai ben noto Smart Working, che permette ai colletti bianchi di svolgere le proprie attività lavorative giornaliere semplicemente utilizzando un computer portatile e rimanendo nella propria abitazione o dovunque preferiscano (si pensi che la diffusione dello Smart Working ha interessato oltre 6,5 milioni di lavoratori in Italia durante la pandemia1). Tale concetto però si può estendere alla fabbrica nel suo intero, raggiungendo le attività di shop floor. In tal senso, grazie alla sensorizzazione degli asset industriali e alla possibilità di aver un costante monitoraggio di questi anche da remoto, molte attività sono state remotizzate andando a concettualizzare il termine Industrial Smart Working.
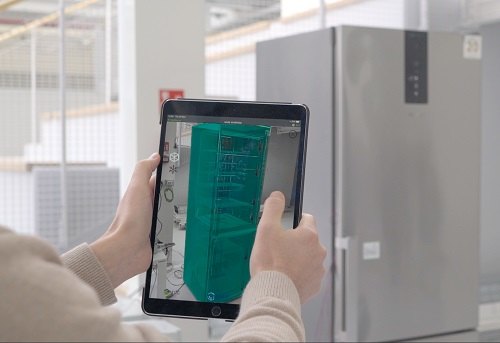
Parlare di solo monitoraggio però può essere limitante in quanto, grazie alle nuove tecnologie di Industria 4.0, anche l’esecuzione delle attività legate alle operation viene abilitata. Tra le tecnologie più rilevanti si vedano: IoT, Autonomous quality, Big data analytics, Cloud computing, Realtà aumentata e Manifattura additiva. Tecnologie, queste, che necessitano un ulteriore livello di integrazione unitamente a una sostanziale attenzione per la cybersecurity.
Come si è già cercato di far intendere poc’anzi, l’elemento innovativo dell’Industrial Smart Working risiede nella capacità di estendere le funzionalità del lavoro flessibile e remoto anche ai contesti più operativi, dove talvolta i ritmi di lavoro sono scanditi da piani di produzione e tempi di ciclo delle macchine. Così come in passato la sfida, vinta, fu di separare la produttività di una macchina dalla forza fisica dell’uomo, oggi l’Industrial Smart Working si pone l’obiettivo di separare la produttività del sistema dalla presenza fisica dell’uomo. L’elemento chiave dell’operatore diviene dunque la competenza, e non la capacità di svolgere mansioni manuali (il contributo alla sfida per una maggiore parità di genere è quindi evidente).
È proprio grazie alla quarta rivoluzione industriale che questa transizione è ora possibile e, come in ogni rivoluzione industriale precedente, è ragionevole pensare a come cambieranno le attività di fabbrica e quale sarà il ruolo delle tecnologie in questo processo.
Per fare ciò è necessario riprendere le già citate tecnologie abilitanti e calarle nei diversi processi aziendali. Tali tecnologie possono essere distinte in tecnologie orientate al controllo e monitoraggio degli asset, come ad esempio l’IoT, tecnologie orientate all’esecuzione dei processi, come l’automazione avanzata, e tecnologie “ponte” tra le prime due categorie e quindi orientate al supporto decisionale, come ad esempio l’intelligenza artificiale.
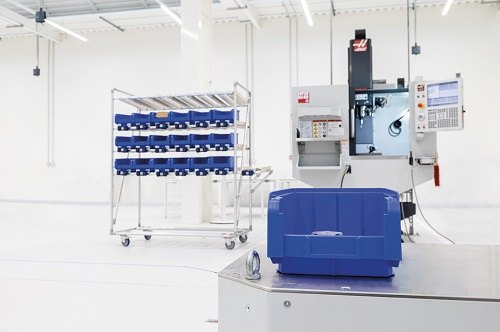
In ambito produttivo, sensori connessi permettono di raccogliere informazioni dalle macchine in tempo reale e archiviarle in database consultabili da remoto. Unitamente a un accesso remotizzato, ai tradizionali sistemi informativi, è dunque possibile recepire informazioni chiave del sistema produttivo e sequenzialmente modificare parametri rilevanti come i piani di produzione. Ciò è a sua volta reso possibile in presenza di sistemi avanzati di automazione dei processi di operation. Non si pensi solo alle attività di produzione, ma anche a quelle di magazzino, tramite AGV (Automatic Guided Vehicle).
Maggiore consapevolezza dello stato delle macchine significa maggiore controllo sui parametri di processo. Ciò racchiude dunque rilevanti opportunità anche per taluni processi laterali come la manutenzione e il controllo qualità. In questi contesti, le tecnologie “ponte” come Intelligenza Artificiale e Machine Learning possono fornire all’operatore o al manager l’adeguata conoscenza per riparametrizzare il sistema produttivo in ottica di riduzione dei pezzi non conformi e riduzione del tempo, e del costo, sostenuto in attività di manutenzione.
Applicazioni di Industrial Smart Working sono ad oggi ancora limitate in numero ed estensione, sia per fattori culturali e organizzativi che per una distribuzione non organica di tecnologie 4.0 abilitanti nel tessuto industriale nazionale.
Un ulteriore quesito che sorge osservando le dinamiche descritte riguarda il layout della fabbrica. Tema, questo, che trova risposte differenti a seconda del livello di virtualizzazione del lavoro e delle specificità delle singole attività. Viene difficile pensare già a una fabbrica totalmente automatizzata o assistita da remoto (spesso nota come dark factory), ma sicuramente il grado di automazione dei processi sarà più esteso. Ciò si concretizza in una maggiore presenza di macchinari autonomi e una riduzione di aree accessibili all’uomo. Linee e aree saranno maggiormente delimitate da gabbie di protezione e corridoi di passaggio. Tablet e dispositivi digitali entreranno nella quotidianità delle persone rendendo necessaria la creazione di spazi di lavoro sempre più simili a torri di controllo.
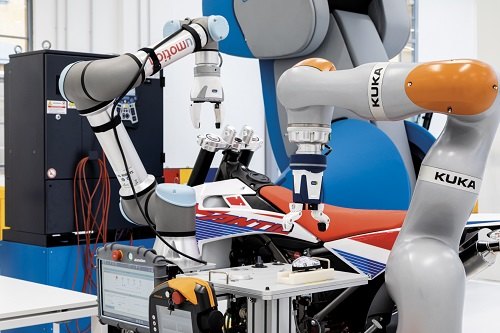
I benefici legati all’adozione diffusa di un modello di lavoro flessibile andranno non solo alle imprese – che potranno ridurre taluni costi fissi, registrare minori tassi di assenteismo e incrementare la resilienza dei propri processi – ma anche ai dipendenti, in grado di migliorare il bilanciamento fra tempo libero e lavoro. Un migliore equilibrio in questo senso, unito a una incrementata sicurezza del luogo di lavoro, è a sua volta motivo di maggiore soddisfazione per le persone con conseguente incremento atteso della produttività.
Le aziende manifatturiere devono però affrontare diverse sfide, tra le quali fornire gli strumenti (hardware e software) necessari a tutto il personale addetto per svolgere la propria attività a distanza, come ad esempio un computer portatile, ma anche garantire un’adeguata formazione che permetta di colmare il digital gap di determinate categorie e generazioni rendendo lo Smart Working realmente fruibile a chi ne necessiti. Industrial Smart Working significa infatti spostare il baricentro delle competenze, da operative e manuali, a digitali. Serve comprendere come supportare tutti i livelli aziendali – da quello manageriale a quello più operativo – verso questo percorso. È necessario partire da un’analisi interna dell’organizzazione attuale e valutare quale sia il percorso più adatto a seconda dei casi. Si noti come non tutte le aziende fossero predisposte a far fronte a tale trasformazione prima dello scoppio della pandemia, ma molte di queste in poco tempo si siano adattate, esprimendo grandi doti di resilienza. Questa trasformazione repentina però deve essere oculata e strutturata, in modo da garantire nel lungo periodo un’ottima qualità del lavoro. Operare da remoto ha infatti comportato in alcuni casi una maggior predisposizione ad allungare le ore lavorative impiegate ogni giorno, nonostante si sia visto come questo possa avere impatti negativi in termini di produttività aziendale2. Considerati i benefici ottenibili, però, non è un caso che il processo di transizione verso modelli di Industrial Smart Working venga oggi spinto sia da aziende che da lavoratori, sebbene esista un grado aggiuntivo di complessità in termini di processo, cultura e normative. Riguardo quest’ultime, è bene ricordare che molti Paesi si sono già adeguati ad accogliere modelli ibridi di lavoro. In particolare, in Italia lo Smart Working è regolamentato dalla legge 81/2017 e dall’art. 4 dello Statuto dei lavoratori. Inoltre, con lo scoppio della pandemia, il contratto collettivo dei lavoratori metalmeccanici è stato rinnovato, al fine di garantire parità di trattamento tra lavoratori dipendenti in presenza e da remoto, assicurando a questi ultimi il diritto di disconnessione.
Infine, lo spostamento verso un modello di lavoro flessibile ed esteso apre nuove sfide organizzative, quali la necessità di ripensare ai modelli di leadership e gestione, ma anche a ricalibrare gli obiettivi dei dipendenti definendo nuovi KPIs (Key Performance Indicators) e meccanismi di incentivazione
NOTE:
01 dicembre 2021